Benefits, challenges, and solutions of recycling electric vehicle batteries.
Even though batteries last many years, they eventually reach the end of their useful life for powering electric vehicles. Policies and incentives for recycling and reusing batteries, including strong health and labor standards, will further lessen the impacts of electric vehicles.
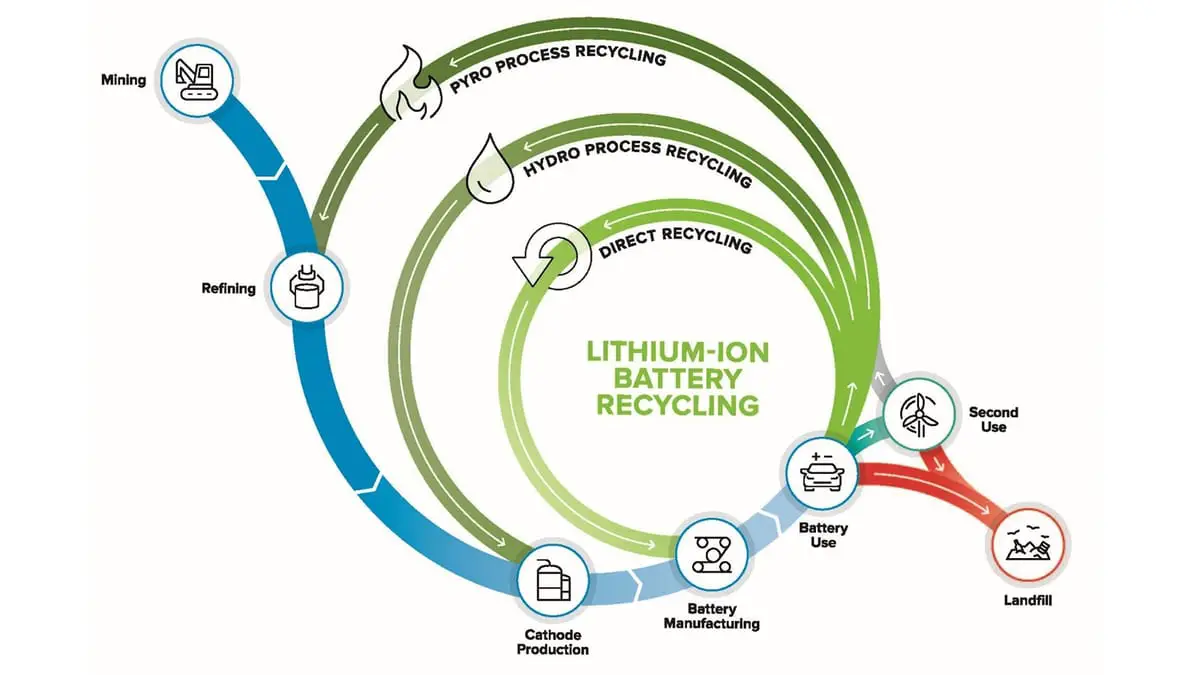
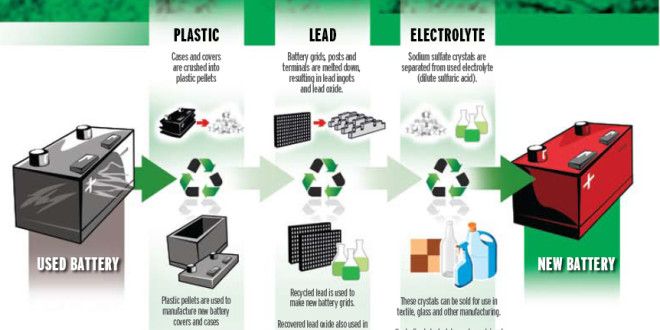
Even though batteries last many years, they eventually reach the end of their useful life for powering electric vehicles. Policies and incentives for recycling and reusing batteries, including strong health and labor standards, will further lessen the impacts of electric vehicles.
It is now clear electric vehicles play a major role in curbing pollution and solving the climate crisis, however, manufacturing them will need requirements that will aid the mass production of the batteries that power them. How batteries are made, what they are made of, and whether they are reused or recycled affect the sustainability of this crucial component. Batteries need a lot of energy in a small package with large quantities of cobalt in lithium-ion batteries.
EVs are much same to conventional cars with less difference which is the battery. The traditional lead acid batteries are easily recycled but for Lithium-ion batteries its not the same because there is no much advocacy on recycling. Electric cars are large and heavy than those in ICEs and contains lithium-ion cells, all of which need dismantling. They contain hazardous materials, and have an inconvenient tendency to explode if disassembled incorrectly.
Benefits of recycling batteries
There are several reasons that you should recycle Li-ion batteries.
i) The recycled materials can be re-used to make new batteries. The materials recovered could be used to make new batteries, lowering manufacturing costs. Currently, those materials account for more than half of a battery’s cost. The prices of two common cathode metals, cobalt, and nickel, the most expensive components, have fluctuated substantially in recent years.
In many types of Li-ion batteries, the concentrations of these metals, along with those of lithium and manganese, exceed the concentrations in natural ores, making spent batteries akin to highly enriched ore. If those metals can be recovered from used batteries at a large scale and more economically than from natural ore, the price of batteries and electric vehicles should drop.
ii) According to Zhi Sun, a specialist in pollution control at the Chinese Academy of Sciences, recycling could reduce the quantity of material going into landfills. Cobalt, nickel, manganese, and other metals found in batteries can readily leak from the casing of buried batteries and contaminate soil and groundwater, threatening ecosystems and human health.
iii) Batteries can have negative environmental effects not just at the end of their lives but also long before they are manufactured. Therefore more recycling means less mining of virgin material and less of the associated environmental harm. For example, mining for some battery metals requires processing metal-sulfide ore, which is energy-intensive and emits SOx that can lead to acid rain.
iv) Less reliance on mining for battery materials could also slow the depletion of these raw materials. Researchers found that world reserves of lithium and nickel are adequate to sustain the rapid growth of battery production. But battery manufacturing could decrease global cobalt reserves by more than 10%.
v) Recycling batteries and formulating cathodes with a reduced concentration of cobalt could help lower the dependence on such problematic foreign sources and raise the security of the supply chain.
Recycling comes with so much challenges such as:-
i) Large fluctuations in the prices of raw battery materials, for example, cast uncertainty on the economics of recycling. In particular, the recent large drop in cobalt’s price raises questions about whether recycling Li-ion batteries or repurposing them is a good business choice compared with manufacturing new batteries with fresh materials. If the price of cobalt drops, recycled cobalt would struggle to compete with mined cobalt in terms of price, and manufacturers would choose mined material over recycled, forcing recyclers out of business. Another long-term financial concern for companies considering stepping into battery recycling is whether a different type of battery.
ii) Battery chemistry also complicates recycling. Since the early 1990s when Sony commercialized Li-ion batteries, researchers have repeatedly tailored the cathode’s composition to reduce cost and to enhance charge capacity, longevity, recharge time, and other performance parameters.
iii) Recyclers may need to sort and separate batteries by composition to meet the specifications of people buying the recycled materials, making the process more complicated and rising costs.
v) Battery structure further complicates recycling efforts. Li-ion batteries are compact, complex devices, come in a variety of sizes and shapes, and are not designed to be disassembled. Each cell contains a cathode, anode, separator, and electrolyte.
vi) Large battery packs that power electric vehicles may contain several thousand cells grouped in modules. The packs also include sensors, safety devices, and circuitry that controls battery operation, all of which add yet another layer of complexity and additional costs to dismantling and recycling.
Recycling solution
To achieve a high recycling rate of 80% with low CO2 we use a hydrometallurgical recycling process. The lithium-ion batteries are first made safe for mechanical treatment, with plastics, aluminum, and copper separated and directed to their recycling processes. And what is left of the battery after these processes are the chemical and mineral components, the ‘black mass’.
The black mass consists of a mixture of lithium, manganese, cobalt, and nickel in different ratios. Of these, nickel, cobalt, and lithium are the most valuable and most difficult to recover. Most of today’s recycling solutions for EV batteries are not able to recover these valuable minerals.
The hydrometallurgical recycling process involves a chemical precipitation methodology that allows scarce minerals to be recovered and delivered to battery manufacturers for reuse in the production of new batteries. This technology was developed by the Finnish growth company CrisolteQ that was acquired by Fortum in January 2020.
Source: i) Mitch.J (2019) It’s time to get serious about recycling lithium-ion batteries
ii) Fortum.com (2019) Lithium-ion Battery Recycling Solution