Is this the right time to quit cobalt batteries for EV?
Electric cars are getting cheaper and their sales are on the rise, but their future success may depend on ditching a key ingredient, the heavy metal cobalt,cobalt appears in most commercial lithium-ion batteries, but it comes at a price.
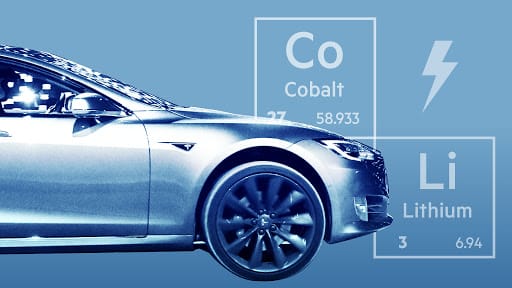
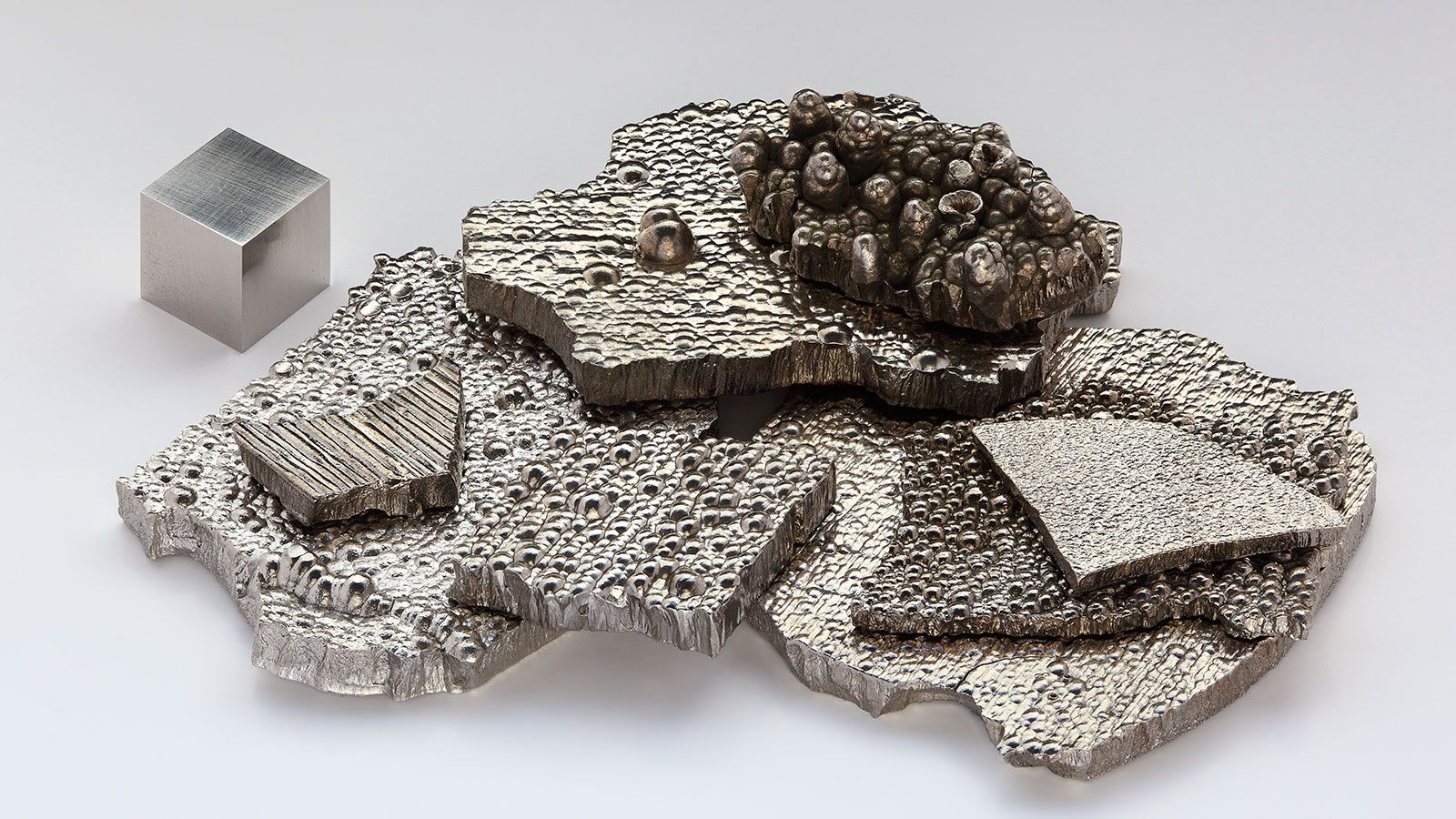
Electric cars are getting cheaper and their sales are on the rise, but their future success may depend on ditching a key ingredient, the heavy metal cobalt,cobalt appears in most commercial lithium-ion batteries, but it comes at a price. The silvery metal is expensive. But it also has a darker cost such as being linked to a long history of human rights violations, including child mining, associated with production in the Democratic Republic of the Congo that accounts to 60 percent.
The mineral is used in the lithium-ion batteries that power electric cars, and demand is steadily rising. A new analysis by Elsa Olivetti at the Massachusetts Institute of Technology and her colleagues has found there maybe cobalt shortages if we don’t start refining and recycling it more efficiently or in greater quantities.
They estimate that global demand for cobalt will rise to between 235,000 and 430,000 tonnes by 2030 – an amount that is at least 1.6 times the world’s current capacity to refine the metal, as of 2016 figures. Lithium-ion batteries used in electric cars and other consumer electronics account for about half of all cobalt demand, and the demand for these batteries is projected to more than quadruple over the next decade.
Cobalt is often produced as a by-product of copper or nickel mining. As such, it is affected by fluctuations in the demand and pricing of those metals. It is also expensive, costing around $33,000 per tonne.The new analysis suggests cobalt supply is adequate at least in the short-term, but that more mining exploration, such as in the ocean, is needed. In addition, we will need to ramp up cobalt recycling by recovering it from batteries in unused electric cars, laptops and mobile phones.
While it is true that cobalt is found in the lithium-ion batteries used in electric vehicles, there is some good news. Electric vehicle manufacturers are transitioning away from cobalt. In fact, Tesla’s current vehicle batteries contain less than three percent cobalt and the company has announced that their next generation of batteries will be cobalt-free.
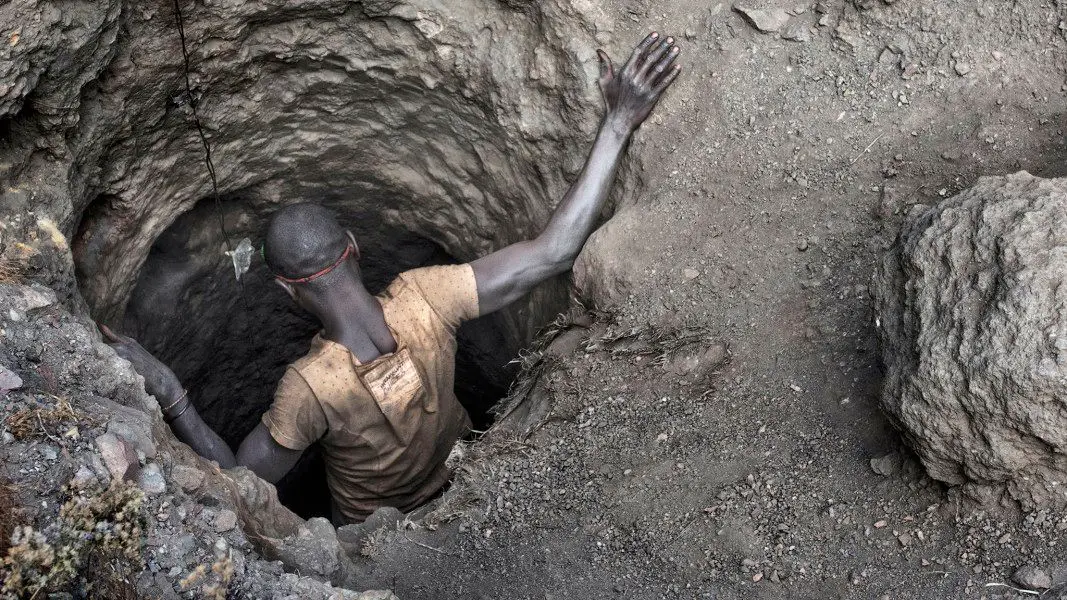
The negative human and environmental consequences of cobalt mining are indeed real and well-documented. However, a serious solution to the exploitation of mine workers involves a comprehensive national trade policy and an economy-wide effort to curtail the use of cobalt.
Another option is to shift to batteries that use less cobalt, or none at all. Elon Musk’s car firm Tesla is in talks with battery manufacturer CATL to use entirely cobalt-free batteries in its China-made cars, according to a report by Reuters. CATL has not responded to the request of Musk publicly
Lithium-ion batteries in electric cars commonly use either nickel cobalt aluminium or nickel manganese cobalt oxides for their ability to offer a long lifespan and high energy density – a determining factor in how far a single charge can power an electric car.
For short-range cars made and sold in China, Reuters says Tesla will instead use lithium-iron-phosphate batteries, which are much cheaper and don’t have the same environmental problems as those needing cobalt. The disadvantage is that these batteries tend to have a lower energy density, reducing how far a car can drive without needing to charge.
Industry analysts such as Simon Moores at Benchmark Mineral Intelligence in London have suggested that the move is unlikely to be replicated outside China, saying it is driven more by a desire to reduce production costs in China than to phase out cobalt.
Lithium-iron-phosphate batteries are already widely used by other Chinese firms, including BYD, the world’s biggest electric car manufacturer. If other electric car manufacturers follow internationally, we may be able to reduce our dependency on cobalt.
Tesla uses a formulation called NCA (nickel, cobalt, aluminum) that is already very low-cobalt. Over the last six years, Tesla and Panasonic ,which supplies batteries to Tesla, have reduced cobalt dependency by about 60 percent already. That’s already very low.
Cobalt is the safe element in the cathode. As you reduce it, you reduce the life cycle of the cell. The current market standard for electric vehicles is an eight-year warranty to retain 80 percent of the original capacity of the battery. You need to be sure your battery can do that, otherwise, you’ll have to replace it under warranty, which is way more expensive than the theoretical savings you gain from less cobalt.
And there’s a safety issue as well. As you decrease the amount of cobalt, you increase the amount of nickel. The cells can overheat and it can no longer effectively cool itself, which can lead to combustion. That’s a relatively low risk but it’s not a risk that can be taken and you need special technology to avoid that. Plus, the low-cobalt formulations need to produce in special dry environments, and so there’s a cost to making them, too.
This can be challenging however the NCA might be dominant in the next 10 years.Electric vehicles are creating a true demand for cobalt now and that’s going to be around for a long time. Demand for cobalt used to be mostly for super-alloys used in jet engines and hardware. Now, over 50 percent of demand is coming from the battery sector, which is going to completely change the industry.