Cobalt Crisis In The Growing EV Industry
Global production of electric vehicles is predicted to top four million cars globally this year, rising to 12 million in 2025. In Europe…
Global production of electric vehicles is predicted to top four million cars globally this year, rising to 12 million in 2025. In Europe alone, 540,000 electric cars will be sold this year, an increase from 319,000 last year. For that to happen, we don’t just need gigafactories to build the batteries but also need to get hold of the key materials, notably lithium and cobalt.
Jaguar Land Rover would pause production on the I-Pace, pinning the blame on shortages at battery maker LG Chem. Lack of battery manufacturing capacity is a key part of this, which is why there is a rush to build gigafactories.
A lack of gigantic factories is a problem that can be relatively easily solved. “In June 2019, there were 91 factories in the pipeline for producing lithium-ion cells around the world, of which around half were already in production the previous year,” says Gavin Harper, research fellow at the Faraday Institution, a battery research group.
That isn’t so easily solved is the issue of getting enough raw materials out of the ground. Harper says it’s been predicted that as demand for electric vehicle surges, there could be constraints around the key strategic elements and critical materials needed for EV battery manufacture in the future.
Aside from the usual hurdles of sourcing and extracting deposits and processing material for use, the key ingredients for EV batteries face geopolitical upheaval including trade wars, local protests, and raise human rights and environmental concerns. That will cause “structural undersupply,” says Andrew Leyland, head of a strategic advisory at Benchmark Mineral Intelligence, and could wreak havoc on EV supply chains just as the industry is hoping to go mainstream.
In Australia, which is now the world’s biggest producer of lithium with China its biggest customer; back in the 1990s, the US was the main lithium supplier to the world, but now it has just one major producer. But just because the lithium isn’t on your land doesn’t mean you can’t get at it. The US does still have small lithium deposits — in particular, around the Salton Sea in California — but deposits in Australia and South America are vast by comparison. But America owns two of the largest chemical companies.
China is globally the biggest player in lithium, no surprise as it’s also making and buying the most EVs. Lithium mines also face protests from farmers in Portugal and indigenous communities in Chile, locking mining efforts in the country, raising questions not only of supply but ethics — with both challenges faced by cobalt.
Unlike lithium, much of cobalt is found in one place, the Democratic Republic of the Congo or DRC — 59 percent of the world’s supply is sourced from that country. Among many concerns, there’s evidence of widespread use of child labor, and last year tech companies were sued for their alleged role in the death and injury of children. Then there’s the harsh economics: cobalt is also one of the most expensive metals in EV batteries, costing between $33,000 and $35,000 per tonne. Research from MIT suggests there’s not enough ability to mine and process the material to meet demand. The research suggests that demand could reach 430,000 tonnes in the next decade, which is 1.6 times today’s capacity.
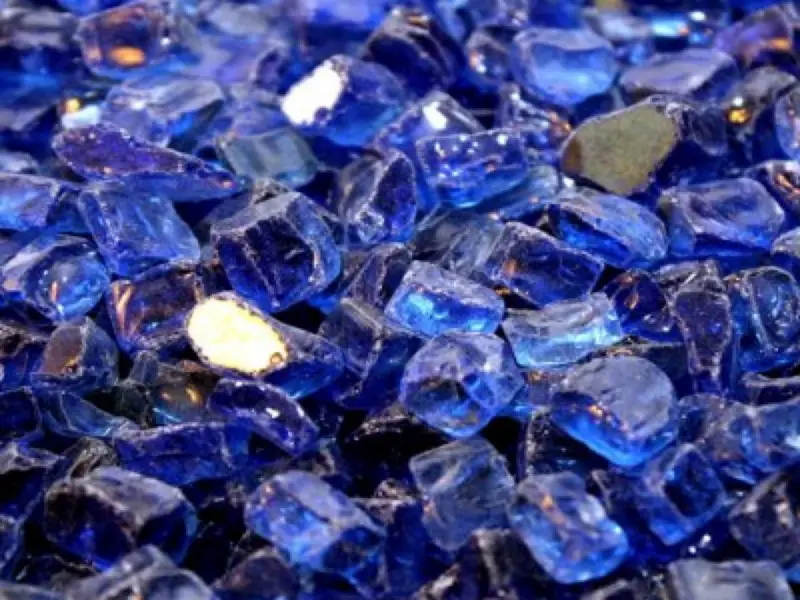
One solution could be finding an alternative to cobalt in EV batteries. One major Chinese manufacturer, Contemporary Amperex Technology (CATL), already produces batteries that use phosphate instead of nickel-cobalt-aluminum or nickel-manganese-cobalt combinations. This attracted the attention of Tesla, with reports suggesting the company is seeking to add lithium iron phosphate batteries to its options.
In 2018, Tesla CEO Elon Musk pledged that his company would stop using cobalt in the next generation of batteries, but the deal in China is likely for shorter-range cars, as phosphate batteries don’t have the same capacity as cobalt ones. We’re going to need better batteries or fix cobalt if EV sales are going to continue to soar.
Regardless of the material in question, one answer to the supply shortage could be recycling, which would help to reduce the environmental impact of EV batteries while also reusing critical materials, we need to to be mine few and processed. Because some of these batteries will go on to live ‘second lives’ in other applications that are potentially less demanding,” says Harper.
But that’s just one solution to a wide-ranging problem. The shift to EVs needs batteries. Right now, their production is the bottleneck, but the next one is likely to be supplied. We can reinvent batteries using different materials, solve the recycling quandary, or simply yank more lithium and cobalt out of the ground — but if the industry doesn’t sort the issue fast, EVs are going to stumble.