Finding a Solution to Fast-Charging Issues
Temperature and humidity levels highly affect the performance, safety, and lifetime of battery cells, thus forging their dominance in a fundamentally provocative situation for battery integration into vehicles.
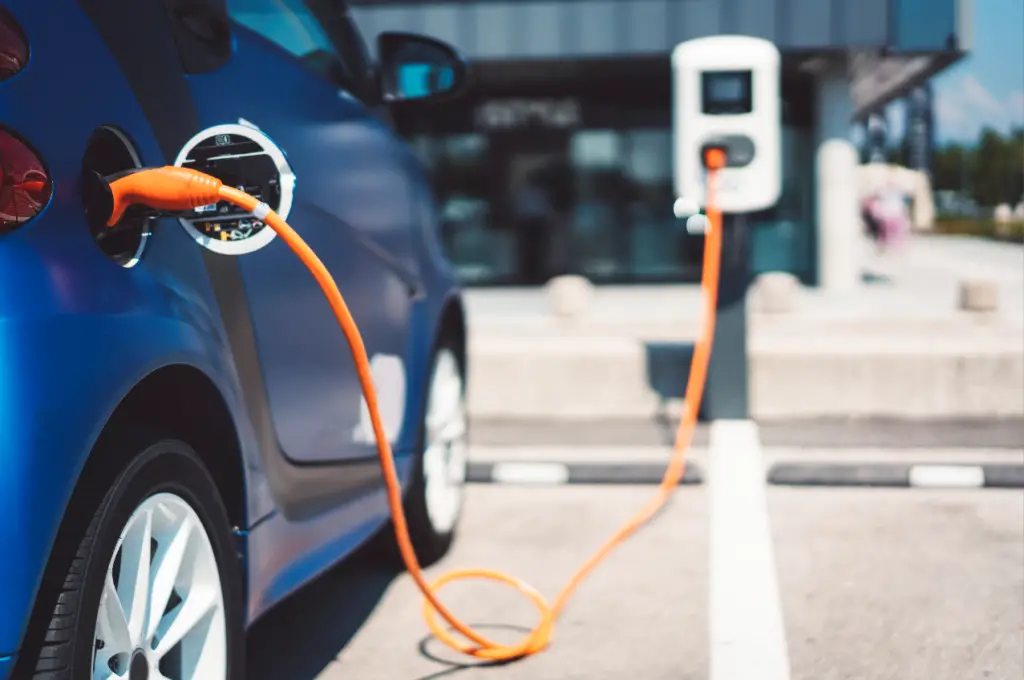
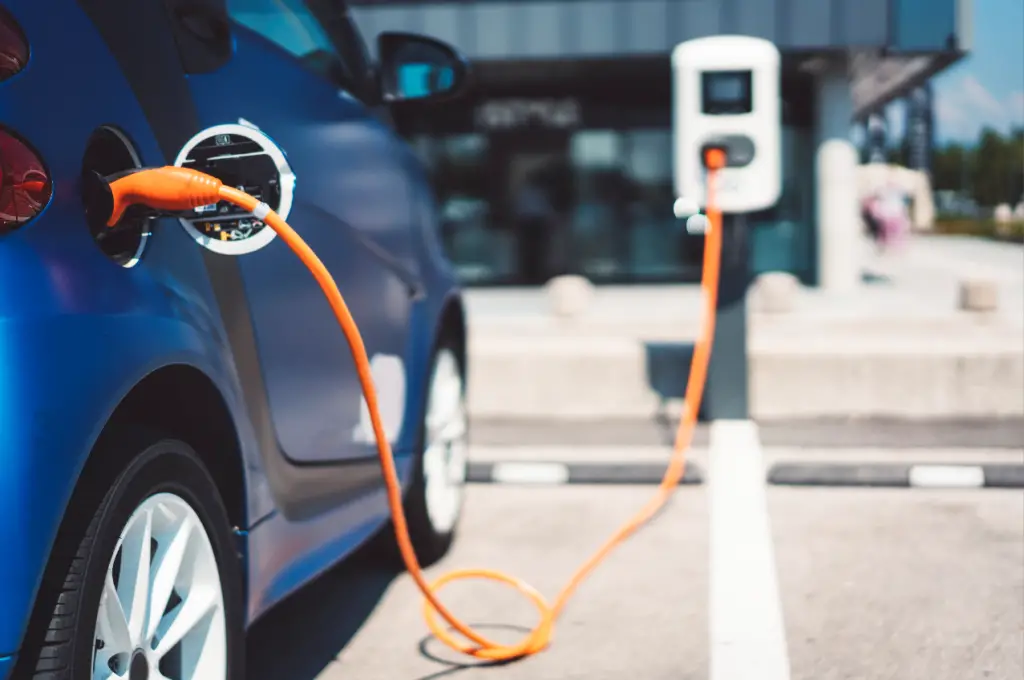
Temperature and humidity levels highly affect the performance, safety, and lifetime of battery cells, thus forging their dominance in a fundamentally provocative situation for battery integration into vehicles. We know all batteries pivot on the electrochemical process whether charging or discharging and by some unspecified means, these chemical reactions hinge on temperature.
Fast charging has its ups and downs to lithium-ion batteries, and resolving this challenge is very important to fight against climate change. Fast-charging solutions can be used to lure more people to ditch combustion-engine vehicles. A study was carried out and put emphasis on lithium-ion electrodes which have tightly packed Nano-sized particles. When charging and discharging cycles, the ions exchange between the anode and cathode leaking into the particles and streaming back out. This continuous exchange makes particles enlarge, shrink and fracture, progressively minimizing their ability to hold a charge. A rapid charging process exacerbates this situation.
Too many high temperatures cause the battery cell to swell due to pressure built inside the cell, gases may be off and the cell may breach and explode. Because of fast charging, thermal management will procure a lot more important for the wholesale vehicle impression.
When the battery temperature is too low or too high, the BMS alleviates the requested current to preserve the health of the battery cells. If the battery pack is equipped with a heating or cooling system the BMS will activate this system to control the cell temperature. Note that battery temperature is not only influenced by the outside temperature, but also by driving and charging as this will generally increase battery temperature.
It is also vital to observe the actions of the nickel, manganese, and cobalt best known as NMC which is common in electric vehicle batteries. The packs soak in lithium ions during discharge and shed them during charging. The study used X-rays from synchrotron a global view of particles going through a rapid charging phase. They then used a scanning X-ray transmission microscope to view individual particles.
Previously scientists thought that variations between electrode particles were not important and the capability to keep and release ions was restricted to how quickly lithium could move within the particles. As we know now from the previous explanation, lithium ions stream out and into all particles simultaneously, at approximately the same pace.
However, there have been new developments that particles themselves manage the pace of lithium ions leaving cathode particles during charging. A few particles shed many of their ions straight away, while others discharge hardly any or no particles at all. The quick-release particles also carry on streaming ions at a quicker rate than slow-release or non-releasing neighboring particles.
Using high-powered observation tools, the findings were that lithium ions move within a lithium-ion battery the study team began to understand the ways lithium ions move within a lithium-ion battery. There is no equal discharging and charging cycles, hence too much pressure on the electrodes and limit their operating lifetime. One of the important things to do is to understand the foundation level it will help to solve the rapid charging challenges.
All said and done, the research will lead to improvements in the cost, durability, storage capacity, and other important things of battery cells from powering electric vehicles to the industrial-scale storage of clean energy.
Designing a lithium-ion battery solution for any application should approach selecting optimum electrochemistry, developing a battery system that meets the application requirements for performance, operating life, electrical and mechanic interfacing and safety, and testing and qualifying the specific operating conditions and abuse scenarios of the application. This development process inevitably means a slow but sure widespread adoption of lithium-ion technology.
For vehicles and infrastructure, must-have new insulators to cope with high charging voltages and power semiconductors resistant to intense heat for charging stations should be emphasized and developed as quickly as possible.
In the future energy companies should focus more on scientific research on electrochemical systems which prove to be packing potential long-term performance and cost criteria for EVs, as opposed to the development of systems based on existing science. Additionally, the charging protocol of the major EV automakers should unify standards as soon as possible worldwide.
It is preferred to purchase the Batteries Electric Vehicles (BEVs) that meet the IEC 62133 safety standard and contain built-in protection circuitry. Do not allow BEVs to be overcharged or deeply discharged. Use manufactured battery cells; do not combine cells in series or parallel. Protect batteries from being broken down, ruptured, or short-circuited.
Go ahead and get battery-specific information from the battery manufacturer about essential voltage, current, and temperature limits, before trying out fast-charging devices. The information, however, might be listed, in detail, on the battery pack or on the box that will have encapsulated the battery.
All things considered, it seems reasonable to assume that fast charging for electric vehicles can be achieved through different approaches where other possibilities are yet to be uncovered. This puts into consideration that the rate at which a lithium-ion battery can be charged is still not fast enough.
All the above are not possible without the battery assurance of safety and healthy battery life. Lithium-ion is a completely clean system that only clutches what it can absorb; it is slowly charged to secure a complete electrochemical reaction.